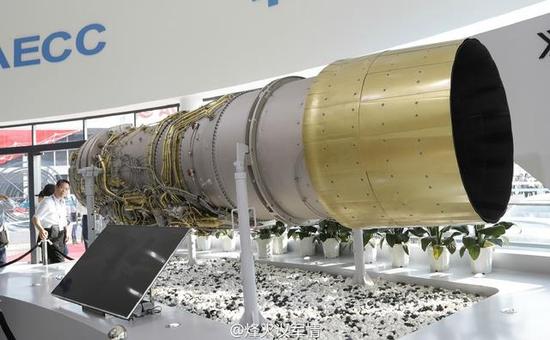
The only countries that can develop the third generation of large thrust turbofan engines are the United States, Russia and China. The successful development and publicity of the Taihang engine proves to the world the overall strength and technical level of the Chinese aviation power industry. It also means that China can achieve independence in the major dynamic areas related to the national economy and people's livelihood.
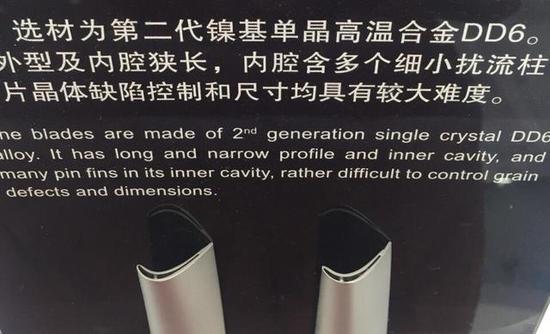
Why are the blades so hard to make? See the details in the above picture. In order to adapt to the high temperature environment inside the engine, the blades are cooled, each blade is precision cast, the inner hollow, and the inner cavity structure is extremely complicated. Whether it is processing or design, it is a huge challenge! !
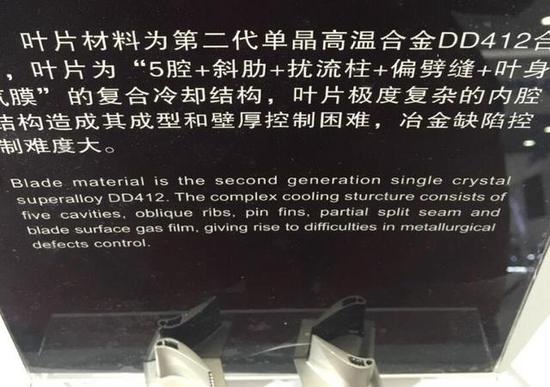
After several decades of development, China's aero-engine blades have formed a relatively complete system, which basically meets the needs of China's advanced aero-engine development; in some new materials (such as directional solidification superalloys, single-crystal superalloys, intermetallic compounds) The development and processing of high-temperature alloys, etc., has gradually kept pace with the world's advanced level.
At present, the development of China's aero-engine blade processing technology faces both valuable opportunities and enormous challenges. To clarify the properties of different blade materials and the intrinsic characteristics of their processing technology, master the technical connotation of blade processing from the theoretical essence and engineering technology, which is the key to master the advanced processing technology of aero-engine blades. China Aviation needs to vigorously promote the basic theory of blade processing technology and the construction of key technology research systems around important issues such as new materials and new processes. This will greatly promote the leapfrog development of advanced processing technologies for aircraft engines in China.
Viton o-rings offer excellent compatibility with a range of chemicals, oils and resist high temperatures up to 400F. Viton o-rings is also known as FKM made of fluoroelastomer one of the most versatile and widely used sealing materials.
Viton O-rings offer excellent resistance to high temperatures, ozone, oxygen, mineral oil, synthetic hydraulic fluids, fuels, aromatics and many organic solvents and chemicals making it excellent for o-ring, gasket and Seal materials. Parker Viton O-rings (FKM O-rings, fluorocarbon rubber O-rings) provide excellent permeability and compression set resistance.
Viton O Ring,Viton O Rings,Rubber Seal O Ring,Rubber Seal Viton O-Rings
Shenyang Guide Rubber Products Co.,Ltd , https://www.guiderubber.com